light industry
Transformation of frequency conversion and speed regulation of mine hoist
2016-05-13
一、survey
The mine hoist is an important equipment in the production process of the coal mine. The safe and reliable operation of the elevator is directly related to the production situation and economic benefit of the enterprise. Shanxi coal mining, coal mining well through the inclined shaft lifting machine for coal will be dragged to the ground. This drive system requires frequent positive, reverse start, deceleration brake, and the speed of the motor must be changed. The mechanical structure of the inclined shaft hoisting machine as shown below. The machine is powered by the winding motor shaft hoist, the rotor series resistance speed.
At present, most of the small and medium mine the inclined shaft winch upgrade, traditional inclined shaft hoist is generally AC winding motor series resistance speed control system, the resistance switching relay, AC contactor control. This control system, due to the frequent movement of AC contactor in the process of adjusting speed, the equipment is running a long time, the main contact of the AC contactor is easy to oxidize, which causes the equipment fault. In addition, the speed control performance of the hoist in the stage of deceleration and crawling is poor, often cause the parking position is not accurate. Hoist frequent starting, speed and braking, in the rotor circuit outside the series resistance of the generation of a considerable power consumption. The AC wound rotor motor series resistance speed control system belongs to a stepless speed regulation, the smoothness of the speed difference; low speed when the mechanical properties of soft, static slip larger; Consuming Resistance slip power rate is large, energy-saving and poor; large starting current impact and shift control process; high speed vibration in the operation of large and poor safety.
二、Transformation scheme
In order to overcome the shortcomings of traditional AC winding motor series resistance speed control system, the variable frequency speed control technology is adopted to improve the constant torque control in the whole frequency (0~50Hz) range. For the treatment of renewable energy, the energy consumption braking scheme with low price or more remarkable regenerative braking scheme can be adopted. For safety considerations, hydraulic machinery brake needs to be retained, and in the design process of hydraulic machinery brake and inverter brake to be integrated. The mine hoist frequency control party as shown in figure:
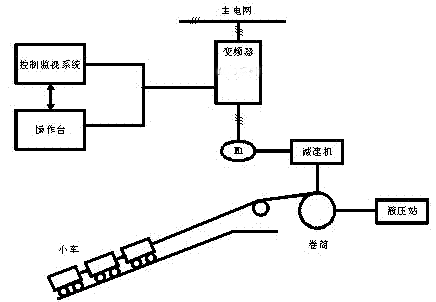
The use of the field around the wire motor, the need to use the inverter to drive the rotor of the three lead out of the short circuit.
三、Program implementation
The load is the friction of the inclined shaft hoist typical load, constant load torque characteristic. Heavy vehicles uplink, the electromagnetic torque of the motor must overcome the load resistance torque, starting, they have to overcome static friction torque motor in an electric state, and work in the first quadrant. In heavy vehicle deceleration, although the slope surface have a downward component, but heavy vehicle deceleration time is short, the motor will still be in regeneration status, work in the second quadrant. When the other column of heavy vehicle up, the motor is in the reverse electric state, working in the third quadrant and fourth quadrant. Also have accounted for 10% of the total running time alone to transport tools or equipment to the downhole motor purely in the second or fourth quadrant. At this time, the motor for long time in renewable power state and need effective braking. Therefore, using the energy consumption braking unit and energy consumption resistance of the braking program.
Hoist load characteristic of constant torque potential load, large starting torque, the inverter when properly redundancy. The high performance of ECF100-G series inverter wei. Due to ascension machine for most of the time in electrical state, only in a few hours with renewable energy generation, connected to the inverter braking unit and braking resistor, you can meet the heavy car down the regenerative braking, to achieve a steady downward. Wellhead and a hydraulic mechanical brake, similar to the electromagnetic brake, the brake for heavy vehicle static brake, especially the heavy truck parked on the slope of the inclined shaft, hydraulic mechanical brake must be made. Mechanical hydraulic brake by the original control system and inverter control, mechanical brake whether braking by frequency inverter reach port control, starting when the inverter output frequency reaches the set value, for example, 2Hz, inverter TA, TB, TC port output signal, said motor torque is big enough, the switch on the hydraulic mechanical brake, heavy vehicles can ascend; deceleration process, when the decline of the frequency converter to 2Hz when expressed in the motor torque is small, hydraulic mechanical brake parking brake. In case of emergency, press the emergency stop button, and the frequency converter is free to stop, the hydraulic mechanical brake will work at once, so that the elevator can stop in the shortest time.
Enhance traditional mode of operation, workers sit in coal mine mouth operation stage, hand manipulation control rod motor positive and negative rotation three speeds. In order to adapt to the operation of the operator, this operation mode, frequency converter using multi-stage speed setting, REV, FWD is set to positive inversion, X1, X2, X3 is set to low, medium and high speed. The principle of variable frequency speed regulation is shown below.
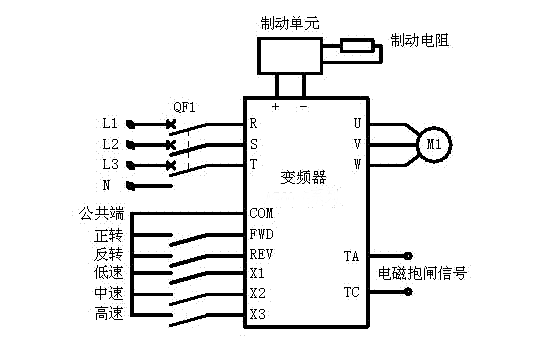
四、Hoist working process
After the frequency conversion and speed adjustment, the working process of the system is not changed. Control rod control motor is three block speed and reverse three speed. Whether the motor forward or reverse, is from coal mine will be dragged to the surface, motor work in forward and reverse electric state, only full trailer near the wellhead and need to deceleration and braking, hoist work sequence diagram as shown in Figure 4.
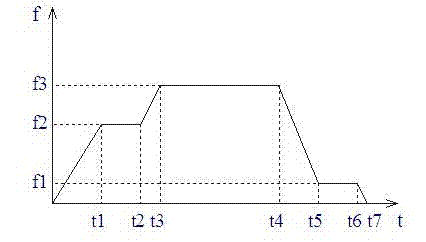
Hoist both forward and reverse its working process is the same, there are seven stages: starting, acceleration and medium speed operation, stable operation, deceleration, low-speed operation, parking brake and so on. Each initiate a run time, the system and the running speed, acceleration and inclined shaft of the depth, the segment acceleration size, depending on the process to determine, the running time by the workers to operate according to the scene of the self. The various stages of the work are described as follows:
(1) the first phase of 0 ~ T1: the train compartment at the bottom of the bottom of the working surface full of coal, a contact signal to the wellhead hoist operator, the operator in reply to a signal to the bottom, and then boot upgrade. The heavy truck from the bottom to up, and began to empty down in the bracket position.
(2) the second stage T1 to T2: heavy vehicle starting and accelerated to inverter frequency f2 speed, medium speed operation time is short, just a transition period, accelerate equipment in time if there is no problem, and then immediately up to normal operating speed.
(3) third stage T2 ~ T3: re accelerated phase.
(4) fourth stage T3 ~ T4: heavy car to the frequency of the frequency converter for the maximum speed of F3 stable operation, the general, this process is the longest.
(5) the fifth stage T4 ~ T5: the operator saw the heavy car fast to the wellhead immediately after the reduction, such as the deceleration time setting is short, frequency inverter braking unit and braking resistance, not due to slow down too fast tripping.
(6) the sixth stage T5 ~ T6: heavy car to slow down to the speed of the inverter frequency of F1 speed crawling, to facilitate the parking in the specified location.
(7) the seventh stage T6 ~ T7: fast to the parking place, the inverter immediately stop, heavy vehicle deceleration to zero, the operator sends a contact signal to the underground, the whole process of the end of the upgrade.
Above for the manual operation, but also according to the operating table automatic operation procedures.
The time of acceleration and deceleration is set in the frequency converter.
五、epilogue
Winding motor rotor series resistance speed control, resistance to consume a large amount of slip power, the lower the speed, the greater the power consumption of the transfer. The use of frequency control, is a kind of non energy efficient way. Hoist the vast majority of the time in the electric state, energy saving is very significant, more than 30% of energy saving, and achieved good economic benefits. Besides, lifting machine variable frequency speed control, stability and security of the system operation are greatly improved, reducing the operation failure and downtime hours, save manpower and material resources, improve the transport capacity, indirect economic benefit is very considerable.