light industry
The successful application of ECF100 series inverter in thermal insulation cotton cotton production
2016-05-12
First, the foreword
Langfang City, Hebei Province, is the largest base of our country rock wool, glass wool production and the flowing water production line using traditional slip speed regulating motor + speed control board + synchronizer to control. At present our company in Langfang City, Dacheng County Shenzhou group's successful transformation of the 3 production line. A production line of 9 sets of production lines, 12 sets of two production lines. The device for automatic large pendulum hammer method of mineral wool production line. In line effective curing 25 meters in length, the cyclone spray dedusting and desulfurization process. After the completion of the transformation, customers are reflected in the use of stable operation, good synchronization effect, high precision. The saving rate can reach more than 35%, the defective rate is greatly reduced than before the transformation, and the yield is obviously improved than before.
Two, flow production line process (see figure below)
Three, electrical system configuration instructions
According to the production process and customer request configuration. The control system to maintain a friendly man-machine dialogue function. By the man-machine interface + MITSUBISHI PLC (FX2N) +ECF100 inverter +ormron rotary encoder. PLC and AC60 inverter (12 sets) Modbus protocol master slave communication. PLC for the host, all inverters are from the machine, there is a unique address. (inverter stack, design for 1-12) is composed of user set operation frequency rate (set operating frequency of the cotton is main frequency) used to send radio instructions to 1# 12# inverter. 2#-12# inverter is used in the main channel (485 communication given) + auxiliary channel given (up and down control) control mode. Encoder control side cutting action and cotton insulation cotton total length calculation. Encoder will collect the number of pulse input to the FX2N high speed count X1 terminals, PLC according to the number of pulses and mechanical deceleration ratio of the actual number of meters, (N=60 (D0) /nt*1000) D0 for the pulse density. To control the side action and the man-machine interface display speed and the total number of meters. But in the man-machine interface according to the production requirements of setting the length of cutting sliver. In order to ensure the blade will cut the finished cotton sliver backward rapidly rolling transmission. Therefore 10# - 12# converter in side instant action should be added to 5HZ frequency based on the existing operating frequency. That is to say, there must be an additional speed function. Acceleration time is about 2S. This system has the general start / stop function, and each transformer has a separate L / micro drop, separate start stop, automatic switching function / hand. To achieve the above functions are dependent on the ECF100 series inverter powerful communication function and the unique main / auxiliary channel frequency of a given model. Need to buy ECF100 inverter 485 module.
Four, the transformation of the scene (see photo)
(the production line side cutting cotton machinery parts)
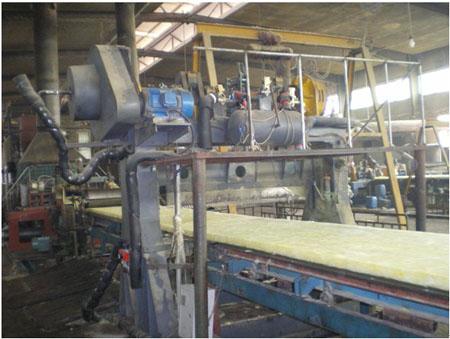
(frequency converter control system)
(man-machine interface)
Five, inverter parameter settings. (2#-12# converter set)
E-01=2 (RS485 communications given run command)
E-02=6 (RS485 main channel frequency is given)
E-03=7 (auxiliary channel up / down for a given - fine tuning)
E-04=0.4 (fine adjustment factor)
E-05=3 {main channel + (K* auxiliary channel)}
H-66=0 (all inverters are from the station)
H-67=2-12 (frequency converter stack address)
H-68=1 parity check (E, 8, 1)
H-69=3 baud rate 9.6kbp
H-70=? Based on the actual situation.
H-72=1 communication is maintained until the new data is received.
Set machine parameter: (velocity)
E-01=2 (RS485 communications given run command)
E-02=6 (RS485 main channel frequency is given)
E-05=0 main channel is valid, and the auxiliary channel is not valid.
H-66=0 (all inverters are from the station)
H-67=1 (frequency converter stack address)
H-68=1 parity check (E, 8, 1)
H-69=3 baud rate 9.6kbp
H-70=1
H-72=1 communication is maintained until the new data is received.
Six, debugging
On the setting method of H-70:
First given each inverter frequency is given independently. E-02=1 arbitrarily determined a main speed (i.e. the set operating frequency of the cotton) unchanged, in feeding, by separate controls for each link inverter frequency, because each link of mechanical reduction ratio is different) for the entire production line in a best state. Allow the operator to confirm that each link at this time for the best. And the record of the inverter frequency (accurate to two digits after the decimal point), each inverter frequency divided by the primary speed frequency value value is the frequency H-70 set, the percentage of communication so that no produced sliver in the process occurs much change (produced a thick cotton and thin cotton variety of specifications), the whole production line are kept synchronized state. This value should be set to set if precise, accurate, UL / micro drop almost no adjustment can meet the production requirements.