light industry
The application of ECF100 in the plastic color of the cloth in the production line
2016-05-13
一、introduction
Plastic color of the cloth is a kind of plastic products, widely used in industry, agriculture, construction, packaging, transportation and other fields. It mainly takes propylene, polyethylene as raw material, through heating, extrusion, scraping, winding, weaving, coating and other processes after the formation of products. Jieyang Shuangfeng film factory mainly produces various specifications of the color of the cloth, this paper with the color of the cloth production line as an example, tells the story of the units of the main production process and production line configuration and corresponding principle, and to David a fly ECF100 series frequency converter as an example, introduces in detail the application of variable frequency speed control technology in the color of the cloth production line.
二、The color of the cloth production process and main equipment
Plastic color of the cloth is mainly to propylene, polyethylene as raw material, by the screw extruder and extruded into the plastic film, plastic film by scraping, heating drawing, shrinking shaping the roll spindle machine rolled into and through the circular loom will thread woven into the color of the cloth, send coating machine into the glue coating treatment, to improve the plastic color of fabric strength, abrasion resistance and waterproof performance, and its production process as shown in figure (1):
三、Each unit of color cloth production line and electric control
By the above color of the cloth production process know, its production line equipment mainly by plastic film drawing machine unit, volume unit, braided unit, coating unit. The following introduces the work principle of each unit and its electrical control method.
3.1 flat film wire drawing machine unit
3.1.1 flat film wire drawing machine unit
Flat film drawing machine unit is the first process color cloth production, is the main raw material particle heating, extruded plastic film. After cooling, scraping, drying, drawing and drawing, the plastic film is rolled up by the receiving unit. The equipment adopts Changzhou into a production company of SJ-65/30 flat film wiredrawing machine, which is mainly composed of a screw extruder, cooling water tank, scraping wire feeding device, a heating device, stretching and forming a device as shown in figure (2). Among them, the main parameters of the screw extruder are as follows:
Screw diameter: diameter 65
Flat film width: 700mm
Screw length / diameter ratio: 30:1
Flat size: 600D ~ 2000D
Screw drive power: 45kW
Maximum extrusion volume: 150kg/h
The raw material is melted and extruded into thin film through the extruder and is cooled by the water tank, and is divided into a wire drawing device. According to the technological requirements of general flat flat, 3 to 5 times the first draft, and then retracting stereotypes about 1 ~ 2%. The unit adopts the three draft, the first stage drafting roller and the second roller drafting realize heating draw forming, the second level and third level to achieve retraction stereotypes wrapped traction heating device schematic diagram as shown in figure (3). Among them, 1 traction, traction 2, traction 3 were driven by three motors, by the three inverter control. According to the process requirement, can adjust the speed of two traction between the units at any time, to achieve the appropriate thread drawing.
图(3)缠绕牵引加热装置结构图
3.1.2 flat film wire drawing machine unit electric control
The control mode of PLC + frequency converter is adopted in the extruder and traction device of flat film drawing machine. Among them, PLC adopts MITSUBISHI FX2N-32MT converter uses6siemens chuangfei Wilson ECF100-G series, a specific type of table (1). Figure (4) gives the drawing unit of the electrical control schematic.
传动单元 |
平膜挤出机 |
牵引1 |
牵引2 |
牵引3 |
电机功率 |
45kW |
11kW |
11kW |
7.5kW |
变频器选型 |
ECF100-T3-045G |
ECF100-T3-011G |
ECF100-T3-011G |
ECF100-T3-07.5G |
控制器 |
FX2N-32MT |
|
|
|
Table (1) wire drawing machine unit frequency converter selection table
Extrusion machine, traction, traction and traction inverter startup and stop is controlled by PLC, the unit speed signal by an external potentiometer given, with the traction and speed thread tension and retraction setting is adjusted according to the technological requirement.
3.2 receiving unit
3.2.1 roll up unit
After heating and drawing, the thread is spun by the winding machine, and the yarn is spun into a spindle. A coiling machine is mainly composed of a rolling unit, a frame, an electric box, a driving mechanism and a spindle.
The winding machine is mainly composed of spindle to form, there are generally three to five. Close coiling machine is composed of four layers of spindle (75 per layer, a total of 300 spindle), each spindle is driven by a 220V three-phase torque motor, spindle torque motor by a torque motor controller control. Can also use Yi Chong Fei ECF300 series inverter and common induction motor instead of torque motor and torque motor controller, the torque control rewinding. The reciprocating traverse mechanism is driven by a three phase 380V asynchronous motor, and is driven by a ECF100 frequency converter to realize the swing frequency movement. In this way, can be uniformly wound on a bobbin thread and bobbin, smooth surface, no convex layer at both ends.
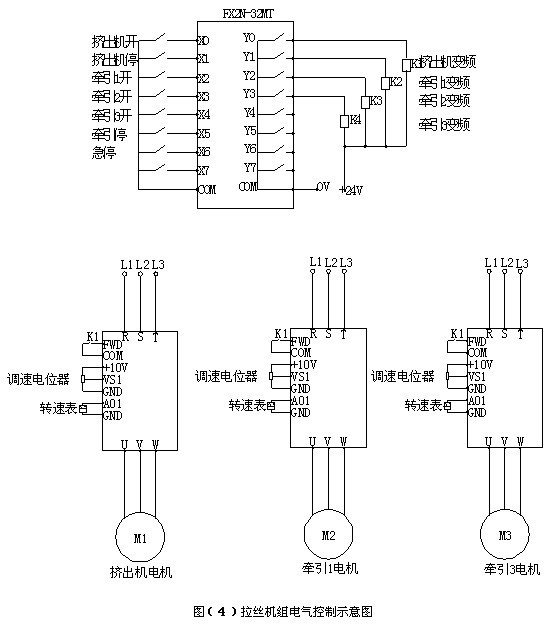
The control mode of the traction roller inverter is the same as that of the extruder, the external terminal is used to stop the control and the external voltage speed control mode is adopted.
Electrical control of 3.2.2 receiving unit
Electric drive coiling machine mainly by the spindle motor and the transverse transmission motor. The spindle motor adopts torque motor, when the wire blocking current does not mutation turn, will not cause the motor burned out. The production line closed rolling machine spindle torque motor controlled by controllable silicon, total motor operating current is about 44a, motor voltage is about 150V. Figure (5) is the schematic diagram of the spindle torque motor control:
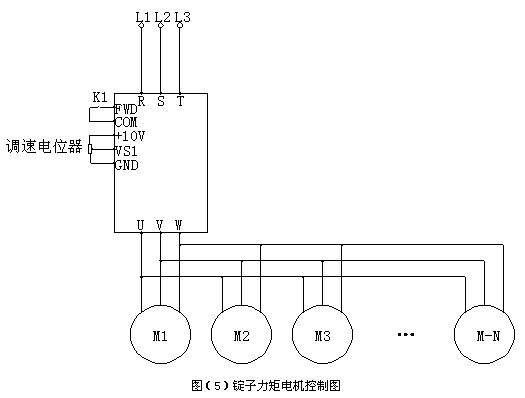
The reciprocating transverse transmission mechanism of the rolling machine is driven by a 7.5kW AC asynchronous motor, which is controlled by the ECF100-T3-7R5G converter. According to the characteristics of the process, the inverter is the swing frequency control function, which can realize silk smooth around the bobbin, at both ends of the thread will not appear convex layer. Through the external terminal to control the starting and stopping of the frequency converter, the frequency is set by setting frequency.
3.3 color weaving unit
Thread winding into ingot are the main supply woven unit, plastic color of the cloth woven currently manufacturers use circular knitting loom weaving. According to the width of the fabric, circular loom generally have four spindle, shuttle, shuttle 8 and 10 shuttle several, mainly by the warp bracket, its frame and weaving device, traction and winding rolls. The weaving device is the main part of the circular loom. The weaving device is composed of a motor, a transmission system, a thread separating mechanism and a pushing shuttle mechanism. The electric drive of the existing production of the new circular weaving machine adopts frequency conversion to realize stepless speed regulation. This paper does not make a detailed description of the working principle of circular weaving machine.
3.4 film forming unit
The silk weaving loom into color cloth, need coating. Mainly is polyethylene or polypropylene as raw material plastic film coated on the color of the cloth, the color of the cloth does not leak, do not glue and improve the strength and wear resistance of the color of the cloth, coated by the coating machine to complete.
Composition of 3.4.1 coating machine
The coating machine is mainly composed of a roll up device, an adjusting device, an extrusion device, an extruder, a cooling device, a cutting edge and a receiving device.
。
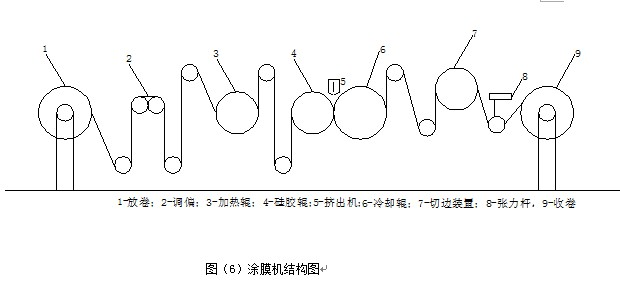
Color of the embryo cloth after heating and 3 preheating, by extruder 5 will melt the molten plastic extrusion, flow to silicone rollers 4 and the cooling roller between the color of the cloth, silicone rubber roller and the cooling roller extrusion coated. The cooling roller roller transmission using variable frequency speed regulation; silicon roller follower roller and the friction between rely on drive; winding and also uses frequency conversion control, according to the position of the tension bar at any time to adjust the winding motor speed. Its electrical control is as follows.
Electrical control of 3.4.2 coating machine
Film machine electrical control part of the extruder screw motor, cooling roller motor and roll motor, all parts of the use of frequency control. Among them, the frequency conversion control method of the extruder is the same as the extruder in the flat film drawing machine. The main is the cooling roller motor and the roller motor speed control. According to the technological requirements and with increase of the close curly size, the volumes of motor speed to gradually reduce, so as to maintain uniform linear velocity. Due to the color of the cloth winding tension on the request is not high, cooling roll and roll by a tension rod to realize constant line speed control. The cooling roller motor is 22kW, 4 pole asynchronous motor, the winding roller motor is 11kW, 4 pole asynchronous motor, and AC62-T3-022L and AC62-T3-011L converter are selected, as shown in figure (7). The cooling roller frequency converter is given a speed regulation signal through an external potentiometer, and the analog output signal (0 ~ 10V) and the Zhang Ligan position feedback signal (-10V ~ 10V) are used as the signal receiving frequency converter. Using double combination function, when tension rod at the equilibrium position is above when coiling frequency increased, when the tension rod is below the equilibrium position collection volume frequency decreased, so as to maintain the cooling roller and winding holding the same line speed.
四、Debugging notes
The color of the cloth production line is composed of a plurality of different units, different requirements of each unit process, so the electrical control is relatively complex. The production line is mostly adopts frequency conversion technology, to use the inverter control functions, debugging should to be familiar with the production process control requirements and the corresponding frequency changer function according to the on-site commissioning should pay attention to the following matters.
4.1 wire winding machine frequency converter type selection
In the selection of frequency converter, we must first understand the characteristics of each unit load, according to the characteristics of the load, select the appropriate frequency converter. In this production line, the coiling machine is replaced by the control torque motor which is controlled by silicon, and the current is about 44A. So here choose AC80 inverter and three-phase induction motor, replace the original torque motor winding scheme. Each inverter drives an ordinary motor, the torque control mode is adopted, the control precision and the response speed are greatly improved compared with the torque motor. With alternative methods can refer to "David chuangfei AC80 vector inverter instead of torque motor applications".
4.2 coating unit roll up debugging
According to the experience of the scene debugging, inverter debugging in general according to the first single after, first light after the heavy "principle, namely in production line equipment debugging, first for each unit of debugging respectively. Each unit debugging normal and unit of the FBI, the first empty debugging after normal load debugging. Due to color of the cloth winding tension on the request is not high, the given signal and tension rod linear superposition method to realize coiling frequency converter control, coiling occasions mostly require the use of belt tension control function of the inverter to control.
五、Summary
The color of the cloth is our life commonly used in plastic products, are widely used, due to the promotion of VVVF technology, all kinds of plastic machinery using VVVF technology, on the one hand, improves the product precision and automation equipment control level and working efficiency, on the other hand reduced equipment maintenance costs, and achieve the energy-saving effect.